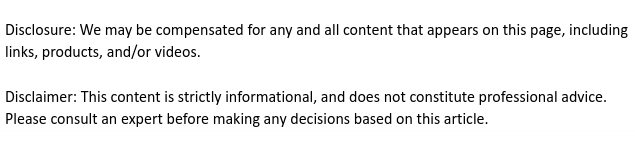
Here in the United States, we’re responsible for almost half of the pharmaceutical market, on a global scale and we’re also globally the largest national producer of chemical products. Chemical companies employ over 800,000 people (this includes the pharmaceutical division as well) and are an important part of the overall industry and manufacturing in the country. However, the materials they’re working with need to be safe for public use or exposure. This oversight is controlled by the U.S Food and Drug Administration and regulations are often grouped under GMP, or Good Manufacturing Practice. GMP quality assurance and GMP quality control ensure that consumers only receive products that are safe and effective to use. If these guidelines aren’t followed, there can be deadly consequences — like in 2012, when almost 50 people died because of a fungal meningitis outbreak that originated at a pharmacy in the Northeast. Ultimately, it was shown that the pharmacy wasn’t following proper cleaning and maintenance procedures, which led to the outbreak.
Tell Me More About GMP
Good Manufacturing Practice essentially means that manufacturers, processors, and packagers of sensitive items like drugs or medical devices (among others) are taking charge to make sure that their products are free from contaminants or tampering, safe for use, and work. Think of these regulations as quality control. Ideally cutting corners, errors, and any mix-ups are eliminated if a company is following GMP. Furthermore, there are strict penalties if a company is found to not be following GMP regulations — products can be recalled or seized, the company may be subject to fines, and employees could face jail time.
Essentially, GMP looks at how companies keep records, how qualified personnel are, standards for cleanliness and sanitation, how companies handle complaints, and equipment verification, among other things.
You may also see “cGMP” which means “current Good Manufacturing Practice.” This is an easy way to remind manufacturers that they need to stay current with the technology and systems being used today. Things that may have been high quality a decade or two ago might not be anymore, based off what systems and technology is being used today.
How Do Chemical Manufacturers Assess Purity?
Purity is especially key for chemical manufacturers. Contaminants can have severe consequences. Diluting a substance or oversaturation can have deadly effects — either too much of something or not enough can kill. Chemical reactions may not act the same if something is impure and lifesaving experiments can be thrown off. Items might be too hard or too malleable if the proportions aren’t correct. Given that chemical manufacturers are releasing these in bulk, they can affect wide swathes of people and products, so it’s important to get it right.
Choosing a quality chemical supplier is a good first step, but afterwards, they may test using the melting point and boiling point. If the disparity between the two is big, that means there’s also a big impurity. Chromatography may also be used to establish purity.
Why Is GMP Storage So Important?
GMP storage conditions will ensure that you’re meeting GMP regulations while items are in transit or waiting to be dispersed to consumers. Proper GMP storage will also keep customers and handlers better protected and any mix-ups or accidents can hopefully be contained quickly and efficiently.
Most GMP storage facilities can be customized, depending on what’s being stored — light, temperature and humidity can be adjusted easily in different rooms. GMP storage will also be in a secure location and will likely be managed by a laboratory information management system, which make sure that items are stable and secure. Monitors and alarms are present at all times.
GMP storage also ensures that items are quarantined until tested or examined, keeping things more secure. In some cases, cryogenic storage might even be available, depending on where you store your items.
Incorporating GMP storage into your manufacturing process helps makes sure that things don’t go awry in one of the last stages before it hits the shelves. Protect yourself and your business by doing the smart thing and looking into facilities.