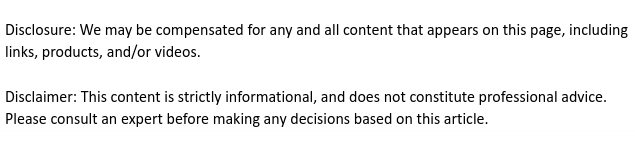

You wake up every day with the weight of the world on your shoulders. Maybe you put cars on the road, or rockets in the sky, or evaluate the safety mechanisms in nuclear reactors. Whatever your niche industry, lives depend on you doing your job well.
As you are no doubt aware, part of making sure you put safe, quality products of this kind out into the world is doing enough reverse engineering and assembly analysis to ensure the design is foolproof. As you are probably also aware, this kind of composite analysis is expensive and often damages the device being tested in the process.
Lucky for you, a group of scientists and engineers in your very field have been working hard on non destructive testing methods. Non destructive testing (NDT for short) amounts to the new frontier of so many highly technical industries. Below are a few fast-growing and valuable NDT analysis techniques:
1. Computerized tomography scanning. Also known as CT or “Cat” scanning. Invented over 40 years ago by a British engineer, CT scanning has become by far the most popular NDT method across multiple sectors. Although we most commonly think of CT scanning as useful in hospitals, this technology is advancing at lighting speeds, and is now capable of producing 3D models of your complex mechanical systems within minutes. It has really come a long way from the two-to-three-hours per a single image once required.
2. Industrial x-ray inspection. X-rays are a form of electromagnetic radiation that have been long used to photograph the insides of the human body. However X-rays, much like CT scans, are also useful in the mechanical industries. X-rays can now achieve a frame rate as fast as 30 per a second, and are able to pick up on your part sizes no matter how large or small. Furthermore when X-raying a machine, one does not have to be as careful as one would be while screening a person, allowing the X-ray technician to achieve the most efficient angles.
3. Ultrasonic testing. Ultrasonic or UT testing is a family of wave testing that is less concerned than the X-ray or CT scan with photography and more concerned with the robustness of material. By far the most common application of UT testing is when one is trying to deduce the thickness or density of internal materials. It can be very useful if your product depends on the structural integrity of a metal, alloy, or concrete foundation.
We don’t know you personally, but we’re more than willing to bet that you’re in the business of pushing boundaries. Some would even call it the business of playing God. Either way, it’s better not to leave any part of your work to chance. Invest in NDT today, and get a little closer to perfection.