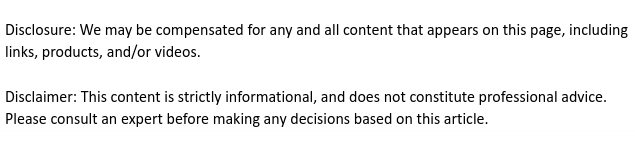
Printed circuit boards, or PCBs, are absolutely essential to the functioning of all electronic equipment from the simplest computer mouse to the vast computer arrays that power space programs. PCB manufacturing has come a long way since the very first such devices. Today’s pick and place machines, or SMT component placement systems, can precision place elements on a printed circuit board at high speed.
What is a Printed Circuit Board?
As its name suggests, this is simply a board made of an insulated material on which electrical circuits are laid in a particular order. The simplest printed circuit board has copper tracks that connect along only one layer and side of surface. The most complicated such boards can be printed on both sides or even in multiple layers of boards. The circuits on either side of the board or between the layers are connected through small holes punched in the insulated materials.
How Does PCB Assembly Work?
The first step to circuit board fabrication is to design the circuit board using a computer program. The idea is to get the most efficient arrangement of circuits possible for running a particular electrical process. Once the board has been designed, a prototype PCB will be printed off using a pick and place machine, and then tested. Assuming the design is right, the printed circuit board manufacturing company will then print off as many as are needed, again using the pick and place machine.
What Is a Pick and Place Machine?
The pick and place machine is a kind of robot that places all the elements on to the board, including resistors, integrated circuits, and capacitors. These machines make circuit board assembly a simple and speedy process, and they have been around since the 1980s.
How Have Pick and Place Machines Changed?
The first pick and place machine was sometimes called a “chip shooter.” The early pick and place machines were not very accurate and could only be used with the simplest components. Although they worked at high speed, engaging a turret to allow the machine to turn around and pick up a part and then place it on the board, the assembly line had to be set up in a sequence to allow for each pick and place machine to do a different part of the assembly.
Over time the costs were too high to continue circuit board assembly in this manner, so pick and place machine designers produced a machine with multiple heads and gantries that could be swapped in and out as needed. These new, far more accurate machines came into use around the year 2000. They could place components on the circuit board with a high degree of accuracy and at enormous speeds.
Modern Machine Development
The newest designs in pick and place machines concentrate on adjusting the software rather than adjusting the heads of the machine in order to efficiently produce different types of printed circuit boards and printed circuit board designs. Updating the software rather than the heads also results in a cheaper production for everyone involved.
As long as we need printed circuit boards the demand to make them smaller, quicker, more accurate will only grow. All the machinery and software involved in PCB manufacturing is constantly under development to ensure that our electronics are as fast and efficient as they can possibly be.